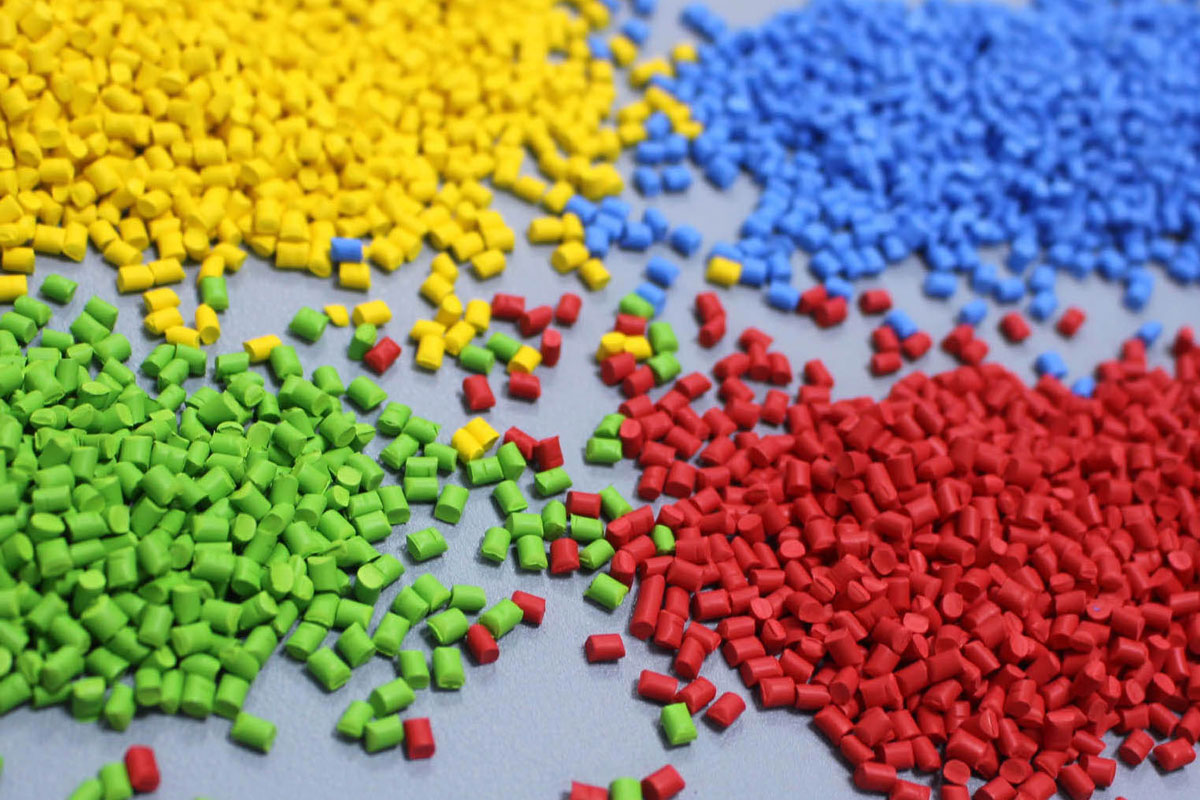
راهنمای جامع برای تولید کنندگان: انتخاب مستربچ مناسب برای تولیدات شما
انتخاب مستربچ مناسب برای تولیدات شما، یکی از تصمیمات مهم در فرایند تولید محصولات پلاستیکی است. مستربچها، ترکیباتی غلیظ و یکنواخت هستند که برای بهبود خواص مختلف پلیمرها به آنها اضافه میشوند. از رنگآمیزی گرفته تا افزایش مقاومت در برابر حرارت، نور ماوراء بنفش و مواد شیمیایی، مستربچها نقش مهمی در تعیین کیفیت محصول نهایی ایفا میکنند.
انتخاب مستربچ مناسب برای تولیدات شما
انتخاب مستربچ مناسب برای یک کاربرد خاص به چندین عامل بستگی دارد که باید به دقت در نظر گرفته شوند. مستربچها برای بهبود ویژگیهای مواد پلیمری استفاده میشوند و میتوانند شامل رنگدانهها، افزودنیهای مقاومتی، و بهبود دهندههای فرآیند باشند.
نوع پلیمر پایه: باید مطمئن شوید که مستربچ با پلیمر پایهای که استفاده میکنید سازگاری دارد. مستربچهای مختلف برای پلیمرهای متفاوتی مانند PE، PP، ABS، PS، و غیره طراحی شدهاند.
نوع کاربرد: مستربچ باید بر اساس نوع کاربرد نهایی انتخاب شود. به عنوان مثال، مستربچهایی برای کاربردهای بستهبندی، لولهسازی، فیلمها، یا قطعات صنعتی مورد نیاز هستند.
رنگ: برای انتخاب مستربچ رنگی، مطمئن شوید که رنگدانههای موجود در آن با استانداردهای شما مطابقت دارد و از نظر مقاومت نوری و پایداری رنگ مناسب هستند.
افزودنیها: ممکن است نیاز به افزودنیهایی مانند ضد اکسیداسیون، ضد اشعه ماوراء بنفش (UV)، آنتیباکتریال، ضد شعله و سایر ویژگیهای مقاومتی داشته باشید. مستربچ باید این افزودنیها را به طور موثری فراهم کند.
درصد مصرف: مستربچها باید با درصدهای مختلفی از پلیمر مخلوط شوند. بهتر است درصد بهینه مصرف برای دستیابی به ویژگیهای مورد نظر را از تامینکننده مستربچ بپرسید.
کیفیت و پایداری: مستربچ با کیفیت بالا به شما کمک میکند که ویژگیهای مورد نظر خود را در محصول نهایی حفظ کنید. همچنین، پایداری طولانی مدت و عدم تخریب ویژگیها در طول زمان مهم است.
مزایای مستربچ برای تولیدات شما
مستربچها به دلیل ویژگیها و مزایای متعددی که ارائه میدهند، در صنایع پلاستیک و پلیمر بسیار پرکاربرد هستند. استفاده از مستربچ، توزیع یکنواخت رنگدانهها و افزودنیها را در پلیمر پایه فراهم میکند و فرآیند تولید را سادهتر و کارآمدتر میسازد. علاوه براین؛ مستربچها میتوانند ویژگیهای فیزیکی، مکانیکی و حرارتی پلیمرها را بهبود بخشند، که منجر به کیفیت بهتر محصول نهایی میشود.
با استفاده از مستربچ، نیاز به استفاده از رنگدانهها و افزودنیهای خام کاهش مییابد که میتواند هزینهها را به طرز قابل توجهی کاهش دهد. همچنین، کنترل میزان مصرف مستربچها آسانتر است. مستربچهای رنگی، رنگهای یکنواخت و بدون ناپایداری را در محصولات پلاستیکی ایجاد میکنند. این یکنواختی باعث بهبود زیبایی و ظاهر محصول میشود. جالب است بدانید که افزودنیهای موجود در مستربچها میتوانند خواص مکانیکی (مانند مقاومت در برابر ضربه) و شیمیایی (مانند مقاومت در برابر UV، ضد اکسیداسیون و ضد شعله) را بهبود بخشند.
مستربچها باعث بهبود فرآیند تولید میشوند و مشکلات مربوط به انسداد ماشینآلات و کاهش راندمان تولید را کاهش میدهند. همچنین، به دلیل کنترل دقیقتر و آسانتر میزان مستربچ مصرفی، میزان ضایعات تولیدی کاهش مییابد. شایان ذکر است که مستربچها به صورت گرانولهایی پایدار و غیرآلوده عرضه میشوند که حمل و نقل و ذخیرهسازی آنها نسبت به پودرهای رنگی یا افزودنیهای مایع بسیار آسانتر و امنتر است.
مستربچها به صورت کنترلشدهتر مصرف میشوند و معمولاً ضایعات کمتری تولید میکنند که به کاهش آلودگی محیط زیست کمک میکند. آنها در انواع مختلفی مانند رنگی، ضد اشعه UV، ضد شعله، آنتیباکتریال، و غیره موجود هستند که این امکان را به تولیدکنندگان میدهد تا ویژگیهای خاصی را به محصولات خود اضافه کنند. مجموع این مزایا باعث میشود مستربچها گزینهای جذاب برای تولیدکنندگان در صنعت پلاستیک باشند، زیرا بهرهوری را افزایش داده و کیفیت محصول نهایی را بهبود میبخشند.
عوامل موثر در انتخاب مستربچ
نوع پلیمر پایه مانند پلیاتیلن، پلی پروپیلن،ABS و غیره باید با مستربچ سازگار باشد تا مخلوط به خوبی با هم ترکیب شده و ویژگیهای مطلوب را فراهم کند.
مستربچها باید بر اساس نوع محصول نهایی (مثلاً فیلم، لوله، قطعات خودرویی، بستهبندی و غیره) انتخاب شوند. هر کاربرد نیازهای خاص خود را دارد که باید در انتخاب مستربچ در نظر گرفته شوند.
برای محصولات رنگی، انتخاب مستربچ مناسب باید به نحوی باشد که رنگدانههای مورد استفاده با استانداردهای رنگی محصول مطابقت داشته باشند. برای محصولات شفاف نیز باید از مستربچهایی استفاده شود که شفافیت را حفظ کنند.
مستربچها میتوانند شامل افزودنیهای ویژهای مانند آنتیاکسیدانها، ضد UV، ضد شعله، روانکنندهها، آنتیباکتریال و ضد استاتیک باشند. انتخاب مستربچ با افزودنیهای مناسب به بهبود ویژگیهای فیزیکی و شیمیایی محصول کمک میکند.
مقدار مستربچ مورد نیاز برای مخلوط با پلیمر پایه بسته به نوع مستربچ و نیازهای کاربردی محصول متفاوت است. درصد استفاده باید به گونهای باشد که بهترین عملکرد را بدون افزایش هزینه اضافی فراهم کند.
کیفیت مستربچ و پایداری آن در طول زمان بسیار مهم است. مستربچ باید دارای گواهینامههای کیفیت باشد و در آزمایشها عملکرد خوبی از خود نشان دهد.
مستربچ باید در دمای فرآیند تولید و شرایط تولیدی (مانند دمای اکستروژن یا قالبگیری) مقاوم باشد و ویژگیهای خود را حفظ کند.
برای محصولات در معرض نور خورشید، رطوبت، حرارت یا مواد شیمیایی، باید مستربچهای مقاوم به این شرایط انتخاب شوند.
مستربچ نباید تأثیر منفی بر خصوصیات مکانیکی محصول (مانند مقاومت در برابر ضربه یا کشش) بگذارد. بنابراین باید مستربچی انتخاب شود که خصوصیات مکانیکی محصول را بهبود بخشد یا حداقل ثابت نگه دارد.
مستربچها باید با استانداردهای صنعتی و بهداشتی مرتبط با محصول نهایی سازگار باشند. برای مثال، در تولید محصولات مرتبط با صنایع غذایی، مستربچها باید از استانداردهای ایمنی مواد غذایی پیروی کنند.
هزینه مستربچ باید با بودجه تولید همخوانی داشته باشد و در عین حال بتواند ویژگیهای لازم را فراهم کند. مقایسه هزینه و کارایی مستربچها میتواند در انتخاب بهترین گزینه موثر باشد.
انتخاب تامینکنندهای که خدمات فنی و مشاورهای مناسبی ارائه دهد، میتواند به انتخاب دقیقتر و بهینهتر مستربچ کمک کند.
انواع مستربچ مناسب برای تولیدات شما
مستربچها انواع مختلفی دارند و بر اساس کاربرد، افزودنیهای مورد استفاده و نوع پلیمر پایه به دستههای متعددی تقسیم میشوند. از جمله:
مستربچ رنگی (Color Masterbatch)
این نوع مستربچ حاوی رنگدانههای آلی یا معدنی است که به منظور افزودن رنگ به محصولات پلیمری استفاده میشود. مستربچهای رنگی به تولیدکنندگان اجازه میدهند تا به رنگهای یکنواخت و با کیفیت در محصولات خود دست یابند.
مستربچ افزودنی (Additive Masterbatch)
این نوع مستربچها شامل افزودنیهایی هستند که ویژگیهای خاصی را به پلیمر اضافه میکنند. برخی از رایجترین مستربچهای افزودنی عبارتند از:
مستربچ ضد UV: برای افزایش مقاومت پلیمر در برابر نور خورشید و جلوگیری از تخریب و تغییر رنگ.
مستربچ آنتیاکسیدان: جلوگیری از اکسیداسیون پلیمر و افزایش طول عمر آن.
مستربچ ضد شعله (Flame Retardant): برای کاهش قابلیت اشتعال محصولات پلاستیکی.
مستربچ آنتیباکتریال: برای جلوگیری از رشد باکتریها و میکروبها روی سطح محصولات.
مستربچ ضد استاتیک: برای کاهش بار الکتریکی ساکن در محصولات پلاستیکی.
مستربچ پرکننده (Filler Masterbatch)
این نوع مستربچ حاوی مواد پرکننده مانند کربنات کلسیم، تالک یا سیلیکاتها است که برای کاهش هزینه تولید و بهبود خواص مکانیکی یا حرارتی استفاده میشود. مستربچهای پرکننده میتوانند سختی، استحکام و پایداری ابعادی را بهبود بخشند.
مستربچ سفید (White Masterbatch)
این مستربچ حاوی دیاکسید تیتانیوم (TiO2) است که به عنوان رنگدانه سفید استفاده میشود. مستربچ سفید برای تولید محصولاتی که نیاز به رنگ سفید یکنواخت و با کدورت بالا دارند، بسیار مناسب است.
مستربچ مشکی (Black Masterbatch)
این نوع مستربچ حاوی کربن بلک به عنوان رنگدانه مشکی است و برای تولید محصولات مشکی با کدورت بالا و مقاومت نوری مناسب استفاده میشود.
مستربچ شفافکننده (Nucleating Agent Masterbatch)
برای بهبود شفافیت و خواص نوری پلیمرهایی مانند پلیپروپیلن استفاده میشود. این مستربچها به کاهش بلورینگی و افزایش شفافیت کمک میکنند.
مستربچهای بهبوددهنده فرآیند (Processing Aid Masterbatch)
این مستربچها حاوی مواد کمک فرآیند هستند که به بهبود جریان پلیمر در طول فرآیند تولید کمک میکنند. این مستربچها میتوانند مشکلاتی مانند چسبندگی به تجهیزات یا افزایش فشار اکستروژن را کاهش دهند.
مستربچهای خاص (Specialty Masterbatch)
این دسته شامل مستربچهایی با کاربردهای خاص میشود، مانند مستربچهای رنگ فلورسنت، مستربچهای عطر و بو (برای افزودن رایحه به محصولات)، یا مستربچهای زیستتخریبپذیر که به سرعت تجزیه میشوند.
مستربچهای مقاوم به حرارت (Heat Stabilizer Masterbatch)
این نوع مستربچها برای محصولاتی که در معرض دماهای بالا قرار میگیرند، طراحی شدهاند و به حفظ خواص پلیمر در دماهای بالا کمک میکنند.
تولید مستربچ چگونه است؟
تولید مستربچ یک فرآیند صنعتی است که طی آن افزودنیها، رنگدانهها و پرکنندهها با یک پلیمر پایه (مانند پلیاتیلن، پلیپروپیلن و غیره) ترکیب میشوند تا محصول نهایی به دست آید. این فرآیند نیازمند تجهیزات خاصی مانند اکسترودر است تا مخلوط یکنواخت و همگن ایجاد شود. در ادامه، مراحل اصلی تولید مستربچ را توضیح میدهیم:
انتخاب و آمادهسازی مواد اولیه:
مواد اولیه شامل پلیمر پایه (به صورت پودر یا گرانول)، افزودنیها (مانند ضد UV، ضد اکسیداسیون)، رنگدانهها (برای مستربچهای رنگی) و پرکنندهها (مانند کربنات کلسیم) هستند. این مواد بر اساس نوع مستربچ و کاربرد نهایی انتخاب میشوند.
مخلوط کردن مواد اولیه:
مواد اولیه در دستگاههای مخلوطکن (بلندر) با یکدیگر مخلوط میشوند. هدف از این مرحله ایجاد یک مخلوط یکنواخت از پلیمر پایه و افزودنیها است. مخلوط اولیه معمولاً به صورت خشک انجام میشود تا توزیع یکنواختی از افزودنیها در پلیمر ایجاد شود.
اکستروژن
مخلوط تهیهشده وارد اکسترودر میشود، جایی که در دمای بالا (معمولاً بین 150 تا 300 درجه سانتیگراد بسته به نوع پلیمر) ذوب و همگنسازی میشود. اکسترودر دارای یک پیچ چرخان (اسکرو) است که مواد را به جلو هدایت کرده و با ایجاد فشار، آنها را به یک توده همگن تبدیل میکند.
خنکسازی و گرانولسازی
پس از اکستروژن، مواد مذاب به شکل رشتههای نازک (استراند) از اکسترودر خارج شده و توسط آب یا هوا خنک میشوند. سپس این رشتهها توسط دستگاه گرانولساز به گرانولهای کوچک (پلت) تبدیل میشوند. این گرانولها همان مستربچ نهایی هستند که برای استفاده در فرآیندهای تولیدی مختلف آمادهاند.
بستهبندی
گرانولهای مستربچ پس از خشک شدن و غربالگری، بستهبندی میشوند. مستربچها در کیسههای مختلف (معمولاً کیسههای 25 کیلوگرمی) بستهبندی و برای ارسال به مشتریان آماده میشوند.
سخن پایانی
انتخاب مستربچ مناسب برای تولیدات شما چگونه است؟ در طول فرآیند تولید، نمونههایی از مستربچ برای تست کیفیت برداشته میشود. تستها شامل ارزیابی یکنواختی رنگ، اندازه گرانول، مقاومت حرارتی، توزیع افزودنیها و سایر خواص مورد نظر هستند. این مرحله برای اطمینان از اینکه محصول نهایی با استانداردهای تعیین شده مطابقت دارد، بسیار حیاتی است.