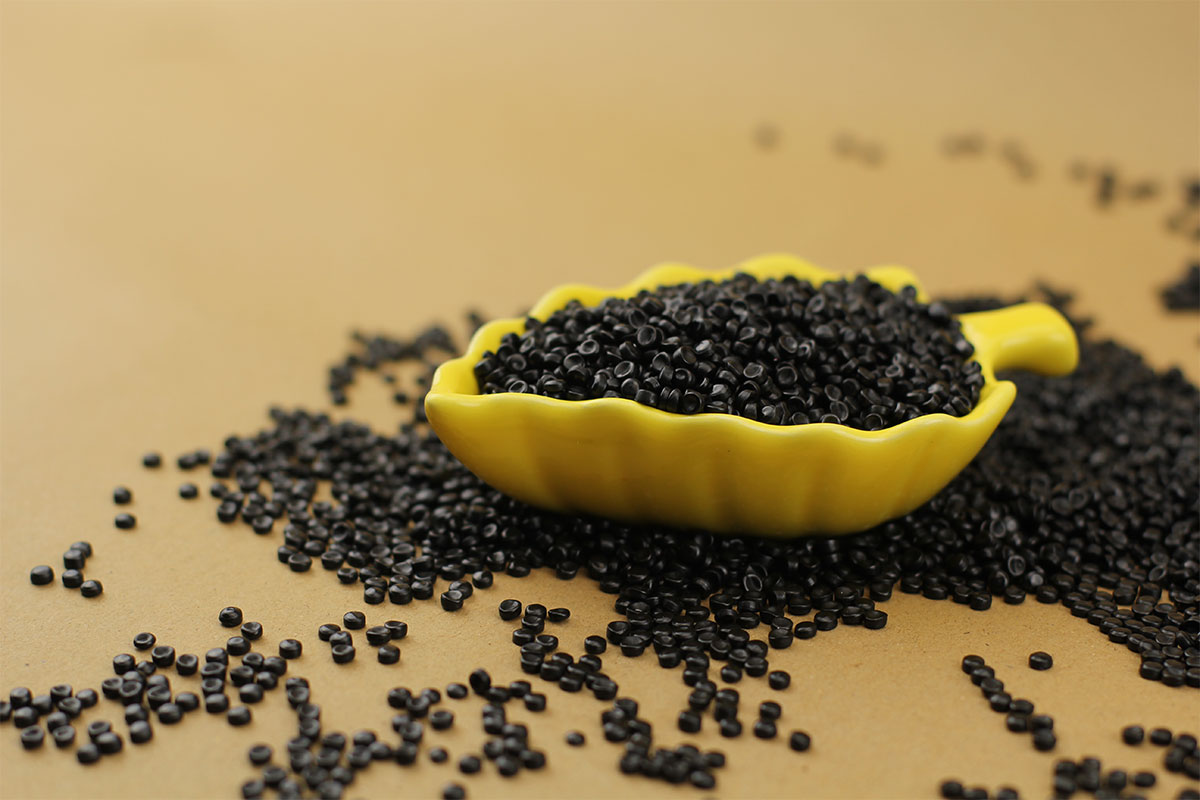
چطور با انتخاب مستربچ درست، کیفیت لولههای پلیاتیلن را چند برابر کنیم؟
انتخاب مستربچ مناسب برای تولید لولههای پلیاتیلن (PE) میتواند تأثیر بسزایی بر کیفیت نهایی محصولات داشته باشد. مستربچها به عنوان ترکیباتی متشکل از پلیمر پایه و مواد افزودنی در فرآیند تولید به کار میروند و میتوانند ویژگیهای فیزیکی و شیمیایی لولهها را بهبود بخشند. در ادامه به بررسی چگونگی انتخاب مستربچ مناسب و تأثیر آن بر کیفیت لولههای پلیاتیلن میپردازیم.
انتخاب مستربچهای با کیفیت بالا
مواد اولیه معتبر: از مستربچهایی استفاده کنید که از مواد اولیه معتبر و با کیفیت تولید شدهاند. این موضوع به بهبود خواص مکانیکی و شیمیایی لولهها کمک میکند.
تولیدکنندگان معتبر: مستربچهای خود را از تولیدکنندگان معتبر و با تجربه تهیه کنید که استانداردهای لازم را رعایت میکنند.
انتخاب مستربچ بر اساس ویژگیهای مورد نیاز
مستربچهای تقویتکننده: برای افزایش استحکام و مقاومت لولهها در برابر فشار و ضربه، از مستربچهای تقویتکننده مانند کربنات کلسیم یا فیبر شیشه استفاده کنید.
مستربچهای ضد UV: در صورت استفاده از لولهها در فضای باز، مستربچهای ضد UV برای جلوگیری از تخریب ناشی از اشعه ماورای بنفش انتخاب کنید.
مستربچهای آنتیاکسیدان: این مستربچها به افزایش پایداری حرارتی و شیمیایی لولهها کمک میکنند و میتوانند عمر مفید لولهها را افزایش دهند.
تنظیم دوز مستربچ
نسبت مناسب: استفاده از مقدار مناسب مستربچ در فرایند تولید بسیار مهم است. نسبتهای زیاد ممکن است باعث کاهش خواص مکانیکی یا رنگ لولهها شود، در حالی که مقادیر کم ممکن است نتوانند تأثیر لازم را داشته باشند.
تجربه و آزمایش: انجام آزمایشات اولیه برای تعیین نسبت بهینه مستربچ در فرایند تولید به شما کمک خواهد کرد.
آزمایشهای کنترل کیفیت
تست خواص فیزیکی و مکانیکی: پس از تولید لولهها، انجام آزمایشات کنترل کیفیت برای بررسی خواص مکانیکی (مانند استحکام کششی و ضربه) و فیزیکی (مانند چگالی و سختی) ضروری است.
تحلیل عملکرد در شرایط واقعی: تستهای دما، فشار و سایر شرایط محیطی میتواند به بررسی عملکرد لولهها در دنیای واقعی کمک کند.
بهبود خواص حرارتی
استفاده از مستربچهای حرارتی: انتخاب مستربچهایی که خاصیت حرارتی خوبی دارند، میتواند به بهبود ویژگیهای حرارتی لولهها کمک کند. این مستربچها به ویژه در کاربردهای دماهای بالا مفید هستند.
رنگ و زیبایی ظاهری
مستربچهای رنگی: انتخاب مستربچهای رنگی با کیفیت میتواند به بهبود ظاهر لولهها کمک کند. توجه به پایداری رنگ و مقاومت آن در برابر اشعه UV نیز مهم است.
توجه به استانداردها
رعایت استانداردهای بینالمللی: اطمینان حاصل کنید که مستربچهای انتخابی با استانداردهای بینالمللی مانند ASTM و ISO مطابقت دارند. این موضوع به اطمینان از کیفیت و ایمنی محصولات کمک میکند.
انتخاب مستربچ مناسب و با کیفیت میتواند بهبود قابل توجهی در خواص و کیفیت لولههای پلیاتیلن ایجاد کند. با توجه به نیازهای خاص تولید، انجام آزمایشات و کنترل کیفیت در هر مرحله از فرایند تولید، میتواند به شما در دستیابی به لولههای با کیفیت و عمر مفید بیشتر کمک کند.
چگونه مستربچ تولید کنیم؟
تولید مستربچ (Masterbatch) فرایندی است که بهوسیله آن افزودنیها و رنگدانهها به پلیمر پایه (مانند پلیاتیلن، پلیپروپیلن و ...) اضافه میشوند. مستربچها به عنوان یک واسطه در تولید پلاستیکها به کار میروند و بهبود خواص و رنگ محصولات نهایی را تضمین میکنند. در ادامه مراحل تولید مستربچ را شرح میدهیم:
انتخاب مواد اولیه
پلیمر پایه: انتخاب پلیمر مناسب (مانند پلیاتیلن، پلیپروپیلن، یا دیگر پلیمرها) بر اساس نوع مستربچ و خواص مورد نظر مهم است.
رنگدانهها: انتخاب رنگدانههای مناسب برای تولید مستربچ رنگی. رنگدانهها میتوانند آلی یا غیرآلی باشند و باید با پلیمر پایه سازگار باشند.
افزودنیها: ممکن است به افزودنیهایی مانند آنتیاکسیدانها، تثبیتکنندهها، یا سایر مواد اصلاحکننده نیاز داشته باشید.
محاسبه نسبتها
نسبت مواد اولیه: نسبت مواد اولیه باید بهگونهای تعیین شود که خواص نهایی مستربچ (مانند غلظت رنگ و خواص مکانیکی) بهینه باشد. این شامل نسبت پلیمر پایه به رنگدانه و افزودنیها است.
خرد کردن و آسیاب کردن مواد اولیه
پودر کردن مواد: اگر مواد اولیه به صورت دانهای یا گرانولی باشند، باید آنها را به اندازههای کوچکتر خرد کرد تا بتوان بهراحتی در مخلوطکردن استفاده کرد.
اختلاط مواد اولیه
مخلوط کردن: در این مرحله، مواد اولیه (پلیمر، رنگدانهها و افزودنیها) با یکدیگر مخلوط میشوند. این عمل معمولاً در میکسرهای خاص (مانند میکسرهای همزن یا برقی) انجام میشود.
مخلوطکردن یکنواخت: هدف این مرحله به دست آوردن یک مخلوط یکنواخت از همه مواد است.
فرآیند ذوب و اکستروژن
اکستروژن: مخلوط آماده شده به اکسترودر منتقل میشود، جایی که با حرارت و فشار ذوب میشود. این فرآیند باعث یکنواخت شدن ترکیب و توزیع یکنواخت رنگدانهها و افزودنیها میشود.
کنترل دما و فشار: در این مرحله، دما و فشار باید به دقت کنترل شوند تا از تخریب مواد جلوگیری شود.
خنککردن و برش
خنککردن: پس از اکستروژن، مستربچ ذوب شده به شکل رشتهای به خارج میآید و به سرعت خنک میشود.
برش به قطعات کوچک: پس از خنک شدن، مستربچ به شکل دانههای کوچک (گرانول) برش میخورد.
بستهبندی و نگهداری
بستهبندی: مستربچها باید در بستهبندیهای مناسب (معمولاً کیسههای پلاستیکی یا سطل) قرار داده شوند تا از رطوبت و آلودگی محافظت شوند.
نگهداری: مستربچها باید در شرایط خشک و خنک نگهداری شوند تا از کیفیت آنها کاسته نشود.
آزمون کیفیت
آزمونهای کنترل کیفیت: قبل از ارسال مستربچها به مشتریان، آزمونهای کیفیت شامل بررسی خواص فیزیکی، رنگ و یکنواختی باید انجام شود.
تولید مستربچ یک فرآیند فنی و علمی است که نیازمند دقت و توجه به جزئیات دارد. انتخاب مواد اولیه مناسب، کنترل دما و فشار در مراحل مختلف، و انجام آزمونهای کیفیت میتواند به بهبود کیفیت مستربچ تولیدی کمک کند. با رعایت این مراحل و نکات، میتوان مستربچهای با کیفیت بالا تولید کرد که در صنعت پلاستیک کاربردهای گستردهای داشته باشند.
فرمولاسیون مستربچ چیست؟
فرمولاسیون مستربچ به ترکیب خاصی از پلیمرها، رنگدانهها و افزودنیهای مختلف اشاره دارد که بهمنظور تولید مستربچهای با ویژگیهای خاص و عملکرد مطلوب طراحی شده است. در اینجا به اجزای اصلی فرمولاسیون مستربچ و نکات مربوط به هر یک از آنها میپردازیم:
اجزای اصلی فرمولاسیون مستربچ
پلیمر پایه
پلیمرها: پلیمر پایه (معمولاً پلیاتیلن، پلیپروپیلن، پلیاستایرن و ...) بهعنوان حامل برای رنگدانهها و افزودنیها عمل میکند. انتخاب نوع پلیمر باید بر اساس ویژگیهای مورد نظر (مانند دما، مقاومت شیمیایی و ... ) باشد.
نسبت: معمولاً پلیمر پایه 40-80 درصد از کل ترکیب را تشکیل میدهد.
رنگدانهها
رنگدانهها: بهعنوان عامل رنگی در مستربچها استفاده میشوند. رنگدانهها میتوانند آلی یا غیرآلی باشند و باید با پلیمر پایه سازگار باشند.
نسبت: معمولاً رنگدانهها 5-20 درصد از کل ترکیب را تشکیل میدهند. نسبت رنگدانهها بر اساس شدت رنگ و نوع کاربرد انتخاب میشود.
افزودنیها
تثبیتکنندهها: برای جلوگیری از تخریب حرارتی و اکسیداسیون پلیمر در حین فرآیند تولید و استفاده نهایی.
آنتیاکسیدانها: برای افزایش پایداری حرارتی و جلوگیری از تخریب پلیمرها.
پلاستیککنندهها: برای افزایش انعطافپذیری و کاهش سختی پلیمر.
مستحکمکنندهها: برای افزایش استحکام مکانیکی و کششی.
مستربچهای ضد UV: برای جلوگیری از تخریب ناشی از اشعه ماورای بنفش.
مستربچهای افزودنی: مانند مواد ضد الکتریسیته ساکن یا ضد باکتری.
نسبت افزودنیها
نسبت افزودنیها معمولاً بین 1-10 درصد از کل ترکیب است و باید بر اساس نوع مستربچ و کاربرد آن تعیین شود.
نکات مهم در فرمولاسیون مستربچ
سازگاری مواد: مهم است که تمام مواد اولیه (پلیمر، رنگدانهها و افزودنیها) با یکدیگر سازگاری داشته باشند تا از جدایی فازها و ایجاد نواقص در محصولات نهایی جلوگیری شود.
تست و بهینهسازی: فرمولاسیون باید بهطور مداوم مورد آزمایش و بهینهسازی قرار گیرد تا به بهترین نتیجه در کیفیت و عملکرد دست یابید.
رعایت استانداردها: مطمئن شوید که تمام مواد اولیه مطابق با استانداردهای بینالمللی و ملی هستند.
مثال یک فرمولاسیون ساده مستربچ
بهعنوان یک مثال ساده، یک فرمولاسیون مستربچ رنگی میتواند به شکل زیر باشد:
پلیمر پایه (پلیاتیلن یا پلیپروپیلن): 60%
رنگدانه (بهعنوان مثال، رنگدانه آبی): 15%
آنتیاکسیدان: 2%
تثبیتکننده: 2%
پلاستیککننده: 5%
مواد افزودنی دیگر: 1-5%
توجه: این نسبتها بسته به نوع مستربچ و نیازهای خاص آن ممکن است تغییر کند.
در مجموع، فرمولاسیون مستربچ یک فرآیند پیچیده است که نیاز به تجربه و آزمایشهای دقیق دارد. با انتخاب صحیح مواد اولیه و تنظیم نسبتهای آنها، میتوان مستربچهایی با ویژگیهای خاص و کیفیت بالا تولید کرد که در صنایع مختلف پلاستیک به کار میروند.
بیشتر بدانید:
- کاربرد پلیمرها در صنعت خودروسازی
- کاربردهای مستربچ سفید در تولید فیلم
- کاربرد پلیمر در صنعت پزشکی و مهندسی پزشکی
- برای تولید لولههای پلاستیکی از چه نوع کامپاندی استفاده میشود؟
کاربردهای مستربچ کدامند؟
مستربچها به عنوان ترکیبات مهم در صنعت پلاستیک، کاربردهای وسیعی دارند. این ترکیبات به بهبود ویژگیها و عملکرد محصولات نهایی کمک میکنند. در ادامه به برخی از کاربردهای اصلی مستربچها اشاره میکنیم:
رنگآمیزی پلاستیکها
افزودن رنگ: مستربچهای رنگی برای رنگآمیزی محصولات پلاستیکی استفاده میشوند. این مستربچها به تولیدکنندگان این امکان را میدهند که رنگهای متنوع و یکنواختی را در محصولات خود داشته باشند.
بهبود خواص مکانیکی
استحکام کششی و ضربهای: مستربچهای تقویتکننده میتوانند استحکام و مقاومت به ضربه محصولات را افزایش دهند. این مستربچها معمولاً شامل مواد مانند فیبر شیشه، کربنات کلسیم و ... هستند.
افزایش پایداری حرارتی
مستربچهای آنتیاکسیدان: این مستربچها برای افزایش پایداری حرارتی و جلوگیری از تخریب حرارتی پلیمرها در حین فرآیند تولید و در طول عمر مفید محصولات به کار میروند.
مقابله با اشعه UV
مستربچهای ضد UV: برای جلوگیری از تخریب مواد پلاستیکی ناشی از اشعه ماورای بنفش در کاربردهای خارجی استفاده میشوند. این مستربچها میتوانند عمر مفید محصولات را افزایش دهند.
کاهش اصطکاک
مستربچهای ضد اصطکاک: برای کاهش اصطکاک در محصولات پلاستیکی، به ویژه در قطعات متحرک و مکانیکی، به کار میروند. این مستربچها میتوانند به افزایش عمر مفید و کارایی محصولات کمک کنند.
مقابله با الکتریسیته ساکن
مستربچهای ضد الکتریسیته ساکن: برای جلوگیری از تجمع بار الکتریکی در محصولات پلاستیکی استفاده میشوند، به ویژه در صنایع الکترونیک و بستهبندی.
افزایش شفافیت و براقیت
مستربچهای شفاف کننده: برای بهبود شفافیت و براقیت محصولات پلاستیکی به کار میروند. این مستربچها بهویژه در تولید محصولات شفاف و نیمه شفاف مانند بستهبندیها مفید هستند.
بهبود قابلیت فرآیندپذیری
مستربچهای پلاستیککننده: این مستربچها به کاهش ویسکوزیته و بهبود قابلیت فرآیندپذیری مواد پلاستیکی در مراحل تولید کمک میکنند.
محصولات بستهبندی
بستهبندیهای غذایی: مستربچها در تولید بستهبندیهای غذایی برای ایجاد خواص خاص مانند ممانعت از نفوذ رطوبت و گازها و افزایش جذابیت بصری به کار میروند.
صنعت خودرو
اجزای داخلی و خارجی خودرو: مستربچها در تولید قطعات داخلی و خارجی خودرو برای بهبود خواص مکانیکی، حرارتی و زیبایی شناسی به کار میروند.
محصولات خانگی و لوازم الکترونیکی
لوازم خانگی: مستربچها در تولید لوازم خانگی برای ایجاد زیبایی، دوام و عملکرد بهینه استفاده میشوند.
انواع مستربچها چیست؟
مستربچها (Masterbatches) ترکیباتی هستند که از یک پلیمر پایه به همراه رنگدانهها یا افزودنیهای دیگر تشکیل شدهاند و بهمنظور بهبود ویژگیها و عملکرد محصولات پلاستیکی به کار میروند. انواع مختلف مستربچها بهواسطهی نوع کاربرد و مواد بهکاررفته در آنها تقسیمبندی میشوند. در ادامه به بررسی انواع مستربچها و ویژگیهای آنها میپردازیم:
مستربچهای رنگی: این نوع مستربچها شامل رنگدانهها و پلیمر پایه هستند و بهمنظور رنگآمیزی محصولات پلاستیکی استفاده میشوند.
کاربرد: در تولید محصولات بستهبندی، لوازم خانگی، قطعات خودرو و غیره.
مستربچهای سفید کننده: مستربچهایی که شامل مواد سفید کننده مانند دیاکسید تیتانیوم هستند و بهمنظور افزایش رنگ سفید و پوششدهی محصولات به کار میروند.
کاربرد: در تولید فیلمها، بستهبندیها و سایر محصولات پلاستیکی.
مستربچهای ضد UV: این مستربچها شامل مواد ضد UV هستند که برای جلوگیری از تخریب ناشی از اشعه ماورای بنفش به کار میروند.
کاربرد: در تولید محصولات پلاستیکی که در معرض نور خورشید قرار دارند، مانند لولهها و قطعات خارجی خودرو.
مستربچهای آنتیاکسیدان: این مستربچها شامل مواد آنتیاکسیدان هستند که به افزایش پایداری حرارتی و شیمیایی پلیمرها کمک میکنند.
کاربرد: در صنایع تولید پلاستیک، بهویژه در محصولات با دماهای بالا.
مستربچهای پلاستیککننده: این مستربچها شامل پلاستیککنندهها هستند که به افزایش انعطافپذیری و کاهش سختی پلیمر کمک میکنند.
کاربرد: در تولید فیلمهای پلاستیکی و قطعات نرم.
مستربچهای تقویتکننده: شامل مواد تقویتکننده مانند فیبر شیشه یا کربنات کلسیم که به بهبود استحکام و مقاومت به ضربه کمک میکنند.
کاربرد: در تولید قطعات مکانیکی، لوازم خانگی و قطعات خودرو.
مستربچهای ضد الکتریسیته ساکن: این مستربچها شامل مواد ضد الکتریسیته ساکن هستند که برای جلوگیری از تجمع بار الکتریکی در محصولات پلاستیکی استفاده میشوند.
کاربرد: در صنعت الکترونیک و بستهبندی.
مستربچهای شفافکننده: این مستربچها بهبود شفافیت و براقیت محصولات پلاستیکی را هدف قرار میدهند.
کاربرد: در تولید بستهبندیهای شفاف و نیمه شفاف.
مستربچهای مخصوص محصولات غذایی: این نوع مستربچها برای تولید بستهبندیهای مخصوص مواد غذایی طراحی شدهاند و باید مطابق با استانداردهای بهداشتی باشند.
کاربرد: در صنایع غذایی و دارویی.
مستربچهای اصلاحکننده خواص: شامل مستربچهایی هستند که به تغییر خواص فیزیکی و شیمیایی پلیمر کمک میکنند، مانند افزایش مقاومت در برابر حرارت، چقرمگی و غیره.
کاربرد: در تولید محصولاتی که نیاز به ویژگیهای خاص دارند.
مستربچها به عنوان ابزارهای کلیدی در صنعت پلاستیک، انواع مختلفی دارند که هر کدام کاربردهای خاص خود را دارند. انتخاب نوع مناسب مستربچ بر اساس نیازهای خاص تولید و ویژگیهای مورد نظر میتواند تأثیر زیادی بر کیفیت و عملکرد محصولات نهایی داشته باشد.
نتیجه گیری
مستربچها به عنوان ابزارهای کلیدی در صنعت پلاستیک، امکان بهبود کیفیت و ویژگیهای محصولات را فراهم میکنند. با توجه به نیازها و ویژگیهای خاص هر محصول، انتخاب مستربچ مناسب میتواند تأثیر زیادی بر عملکرد نهایی و رضایت مشتری داشته باشد.